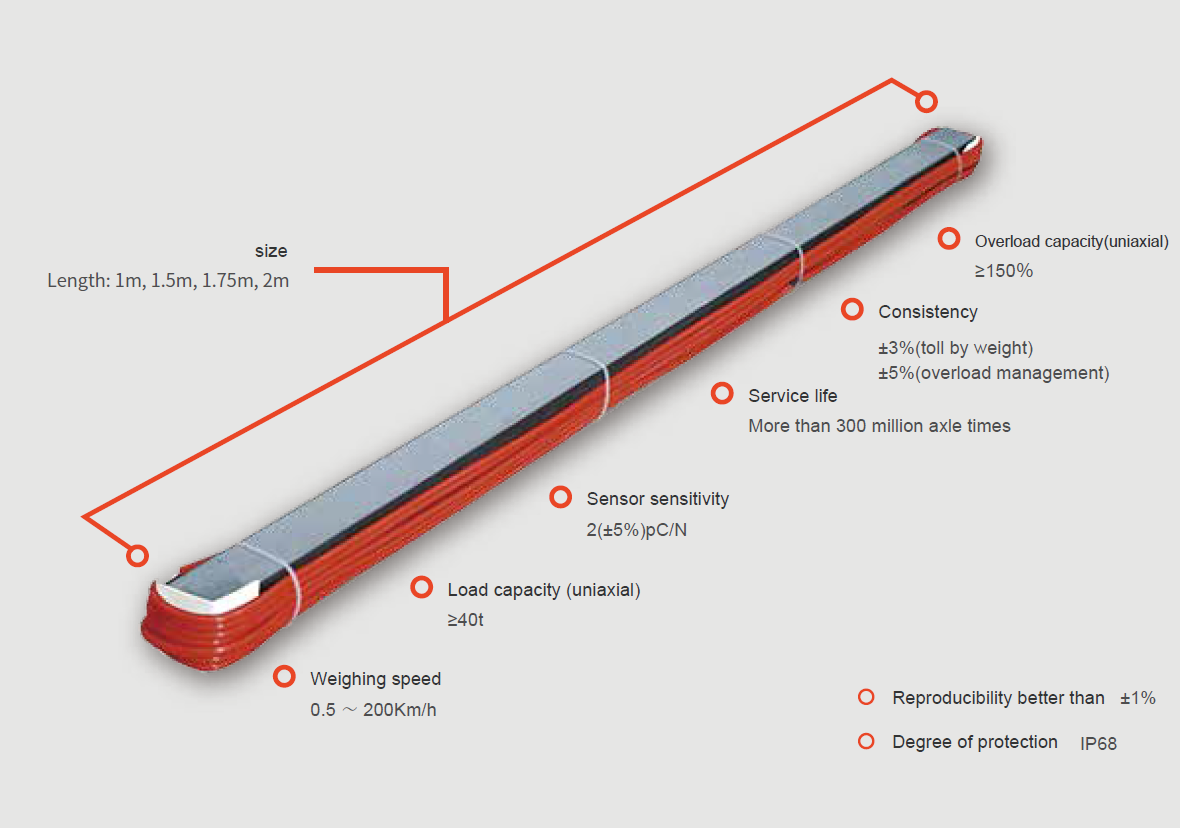
Overloading and exceeding limits of highway vehicles cause significant damage to road surfaces and pose a high risk of safety accidents, a particularly serious issue in our country where 70% of road safety incidents are attributed to vehicle overloading and exceeding limits. This results in direct economic losses of nearly 3 billion RMB, with losses from vehicle overloading and exceeding limits on highways exceeding 30 billion RMB annually. Hence, it's critically important to monitor and supervise overloaded vehicles on highways.
In order to regulate vehicle overloading without disrupting traffic, the Weighting In Moving (WIM) highway dynamic weighing scheme has emerged. This system utilizes piezoelectric quartz sensors to quickly measure vehicle weight as vehicles pass over the road surface at high speeds (<120km/h) and trigger monitoring cameras for photographing.
Enviko quartz sensors are specially designed for low-cost, high-performance piezoelectric quartz sensors for highway dynamic weighing and bridge protection. Constructed with high-strength aerospace aluminum alloy and precision machining, these sensors possess high compressive, tensile, bending, shear, and fatigue load resistance. Through aging treatment, sensor sensitivity remains stable for decades.
Internally filled with special elastic insulating paste, Enviko quartz sensors maintain stable internal pressure, effectively blocking moisture, with a typical insulation impedance value of 200GΩ.
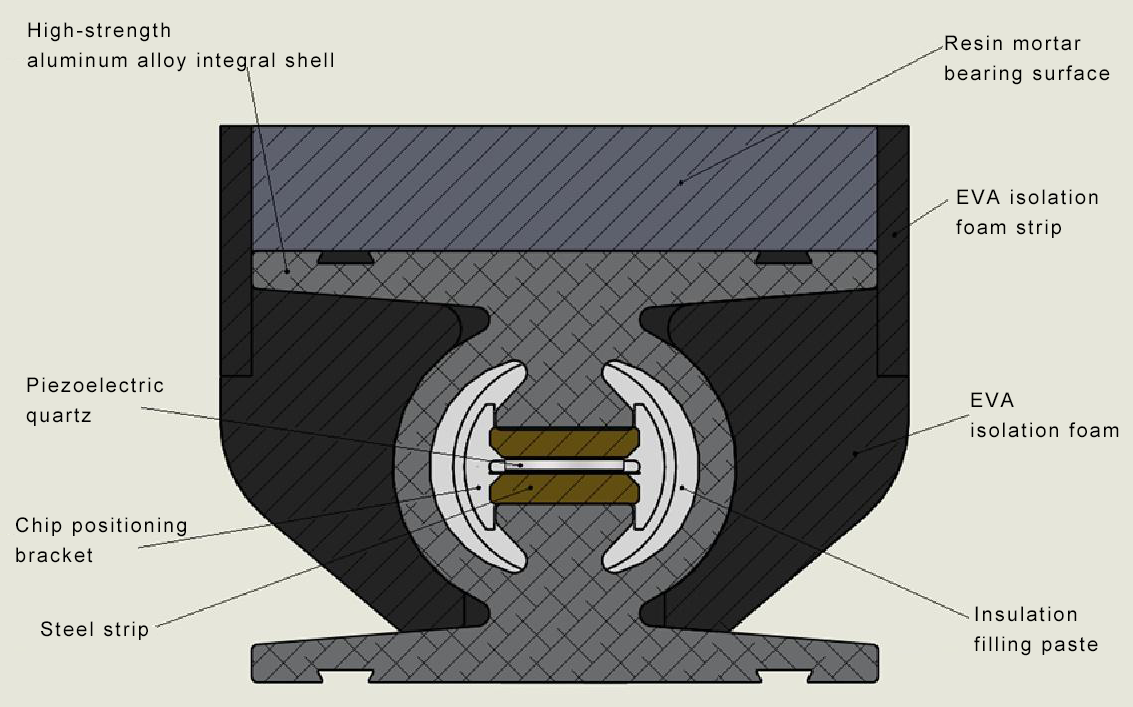
Embedded in the road surface, when vehicles pass over, the wheels press down on the sensor's bearing surface, causing the quartz crystals inside the sensor to generate charge due to the piezoelectric effect. The charge is then amplified by an external charge amplifier into a voltage signal, which is directly proportional to the pressure applied to the sensor. By calculating the pressure signal, the weight of each wheel and thus the total weight of the vehicle can be obtained.
The pressure-charge ratio characteristic of piezoelectric quartz sensors remains unchanged regardless of temperature, time, load size, and load speed. Therefore, even when vehicles pass over the measuring surface at high speeds, quartz sensors can maintain high measurement accuracy.
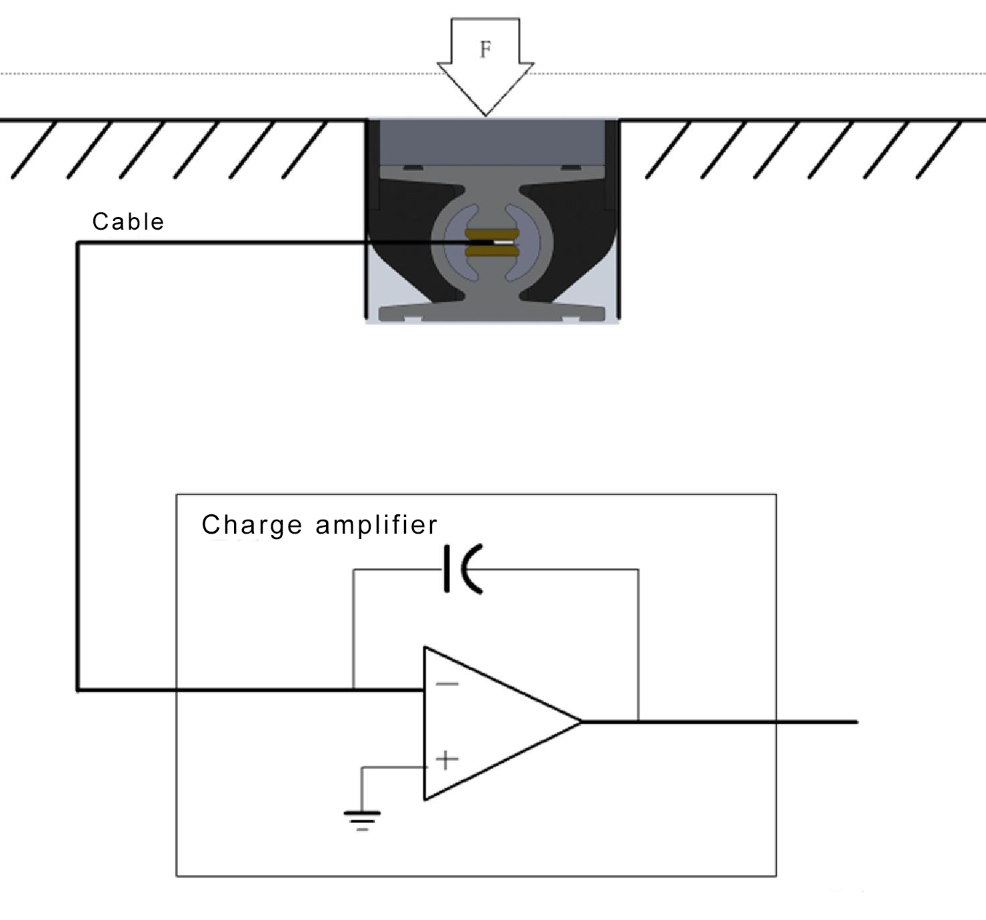
After WIM sensors are embedded in the road surface, they undergo exposure to sunlight, rain, and wheel pressure, making reliability testing crucial.
Temperature and Humidity Cycling Test:
Sensors with bearing surfaces are placed in an environmental test chamber for -40℃ to 85℃ temperature and humidity cycling tests for 500 hours. During the test, the insulation impedance of the sensors must not be lower than 100GΩ. After the temperature and humidity cycling test, the sensors undergo insulation protection and fatigue load testing.
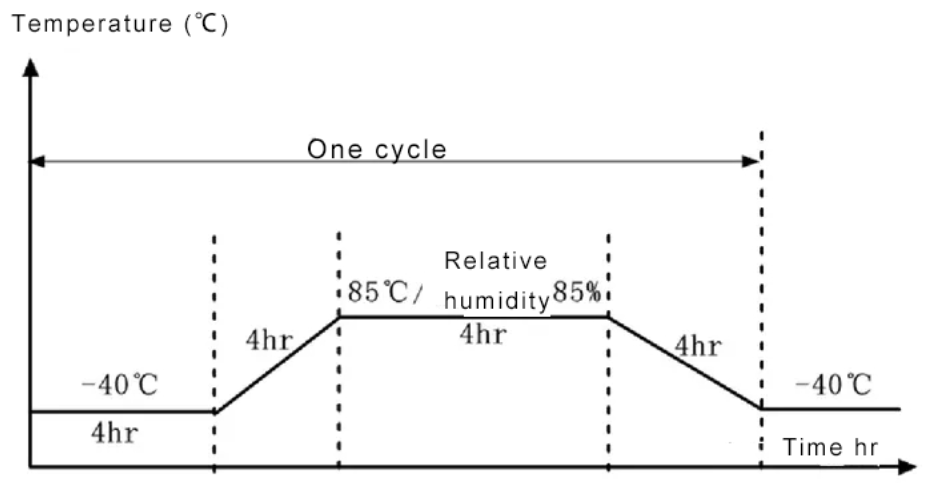
Fatigue Load Test:
A load fatigue test applies a cyclic pressure of 6000N using a steel pressure head with a width of 50mm x 50mm at three positions on the sensor's ends and middle, with loading and unloading once per second, totaling 1,000,000 fatigue loads. The sensitivity variation of the loaded test positions must be <0.5%, and there should be no damage or detachment of the bearing surface.
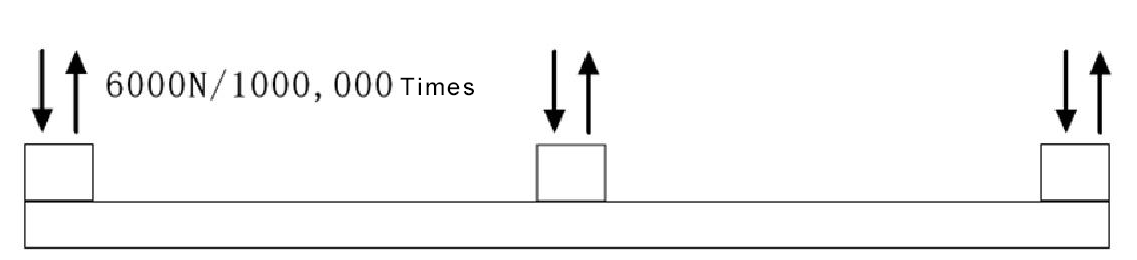
Insulation Protection:
The insulation protection test involves fully immersing the sensor in water, cycling between room temperature and 80℃, with a total test duration of 1000 hours. Throughout the entire test, the insulation resistance of the sensor must not be lower than 100GΩ.
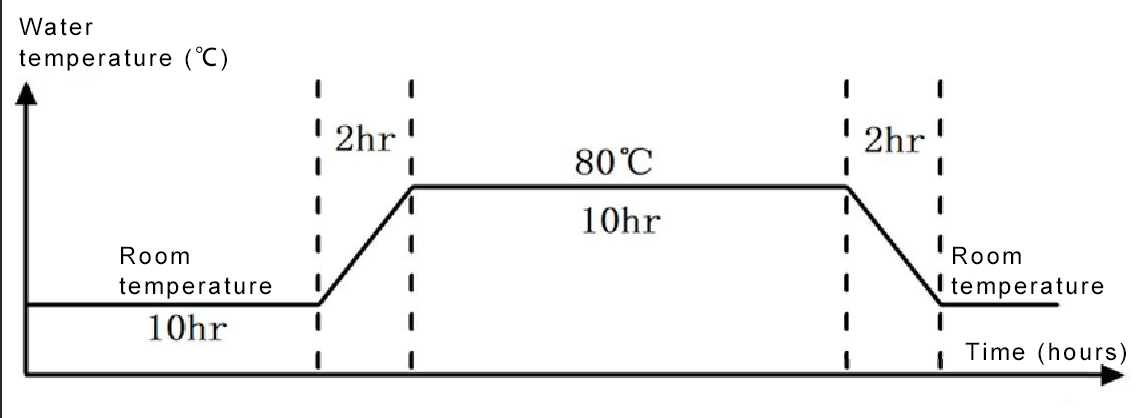
The linearity of piezoelectric quartz sensor signals is a critical indicator of manufacturing processes and accuracy. Excellent piezoelectric quartz sensors ensure FSO<0.5% across the entire range. For WIM sensors, the sensitivity error at any position along the length of the sensor must not exceed 2%. Therefore, strict and accurate sensitivity testing equipment is essential for sensor manufacturing.
The loading characteristic curve measures the force-charge curve and linearity error (%FSO) during loading and unloading with a width of 100mm loading head applied to the sensor at any position.
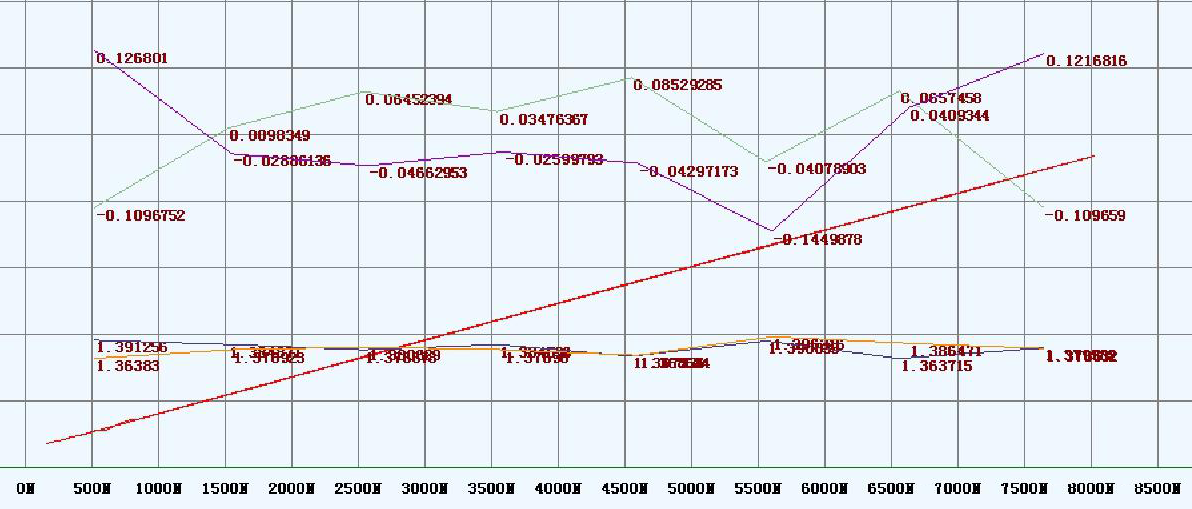
The signal flatness characteristic curve measures the sensitivity value during loading along the length direction of the sensor (without the bearing surface) using a 50mm width pressure head with a force of 8000N, with sensitivity values obtained at each loading test point used to calculate the signal flatness along the length direction of the sensor.
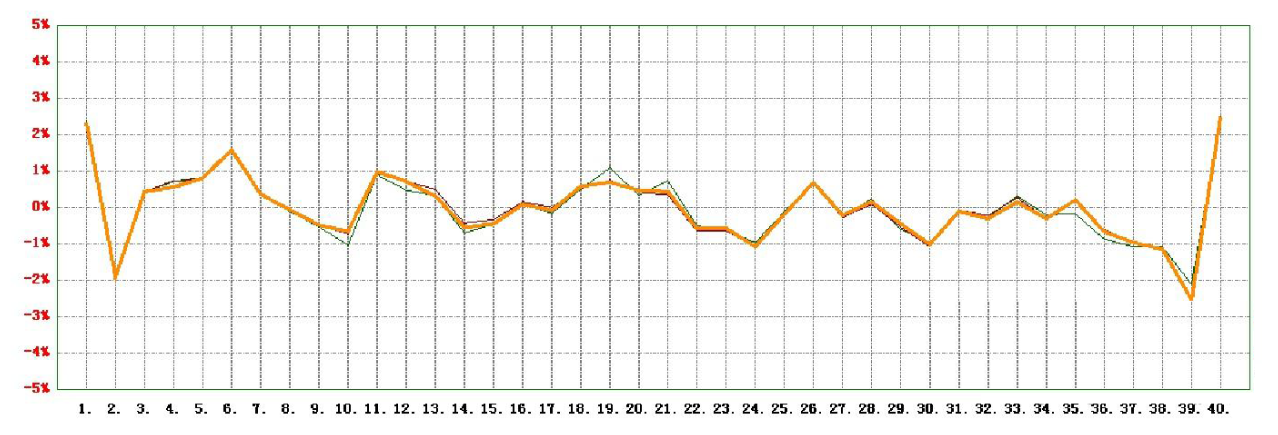
However, some manufacturers deliberately use a 250mm width loading pressure head for signal flatness testing, equivalent to 5 times averaging of the characteristic curve, resulting in falsified accuracy of 1%. Only signals obtained by loading measurements using a 50mm width pressure head can truly reflect the accuracy and quality of the sensor.
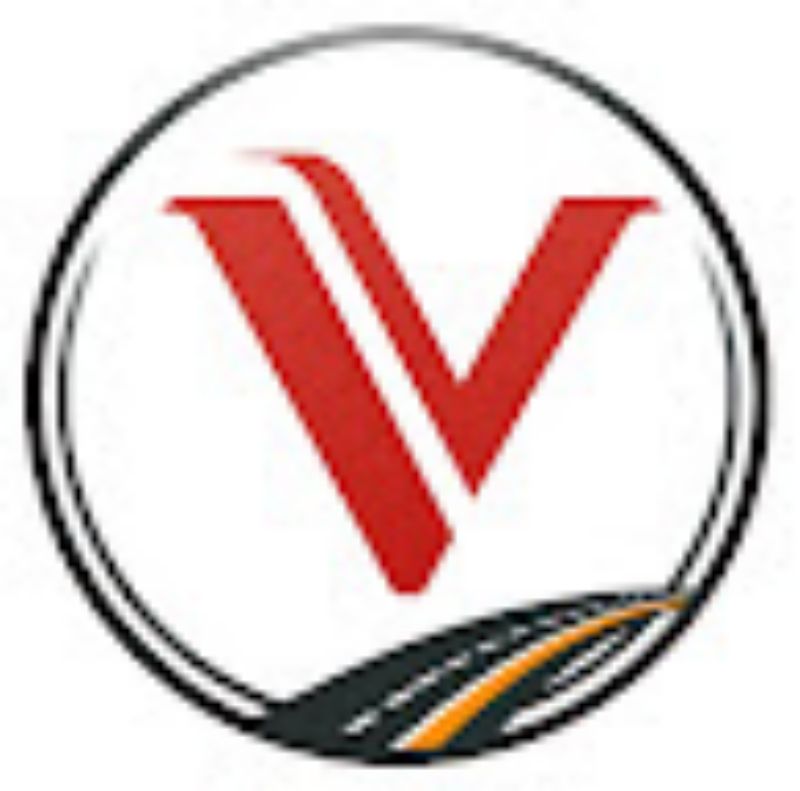
Enviko Technology Co.,Ltd
E-mail: info@enviko-tech.com
https://www.envikotech.com
Chengdu Office: No. 2004, Unit 1, Building 2, No. 158, Tianfu 4th Street, Hi-tech Zone, Chengdu
Hong Kong Office: 8F, Cheung Wang Building, 251 San Wui Street, Hong Kong
Factory: Building 36, Jinjialin Industrial Zone, Mianyang City, Sichuan Province
Post time: Apr-08-2024